Info/FAQ
Info/FAQ
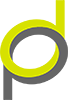
The Waste Plastic Problem
“Of all the plastics that have ever existed, more than half was produced in the last 15 years … and 91% has never been recycled.”
“By 2050, there will be more plastic in the ocean by weight than marine life.”
“According to the 2016-17 National Plastics Recycling Survey (Australian Department of Environment and Energy), approximately 3.51 million tonnes of plastics and plastic products are sold annually in Australia, equivalent to 140 kg per person.
These plastic products are commonly split into two broad classes as follows:
- 37% durable plastics (rigid and semi-rigid plastic containers)
- 63% packaging plastics (mostly film and wrap)
Of these 3.51 million tonnes of plastic entering the market, 88.2% remains unrecovered, with the remaining 11.8% being classified as recycled.”
The above quotes are some of the thousands that seek to inform those that are prepared to listen that our planet is in crisis with plastic pollution.
PlasTech Recycling Limited recognises that the issue is not just one of improving recycling capability, but there is a desperate need to curb the exponential growth of new plastic being manufactured and legislate to make the manufacturers of plastics be accountable for the whole life cycle of the products they produce.
Consumers, businesses, and government at all levels need to reduce their dependency on plastics so that the continued growth of plastics being produced is stopped; or, at the very least, brought under control.
Understanding the above, there are literally billions of tons of waste plastic around the world that need to be cleaned up from the environment on land (in stockpiles, landfills, and loose in the environment ) in our waterways and oceans.
The world has been calling out for a simple solution to enable the economic recycling/upcycling of waste plastics to start to address this global issue.
PlasTech Recycling Pty Ltd’s PlasTech’s PolyWaste Technology has been designed to play a pivotal role in:
- Re-purposing the billions of tons of mixed and contaminated waste plastic already in the environment.
- Divert plastics from the end of life outcomes in existing waste management of plastic processes for manufacture into useful and fully recyclable products.
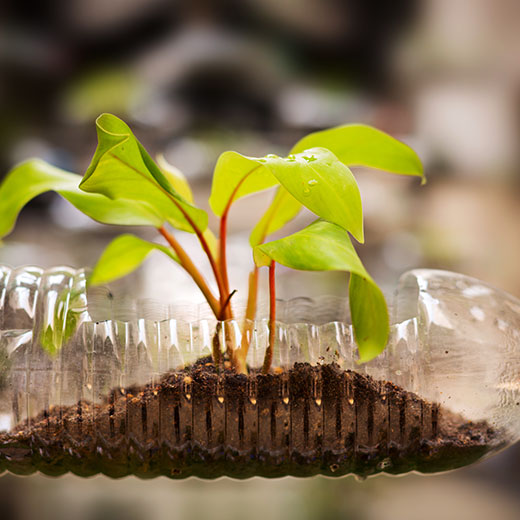
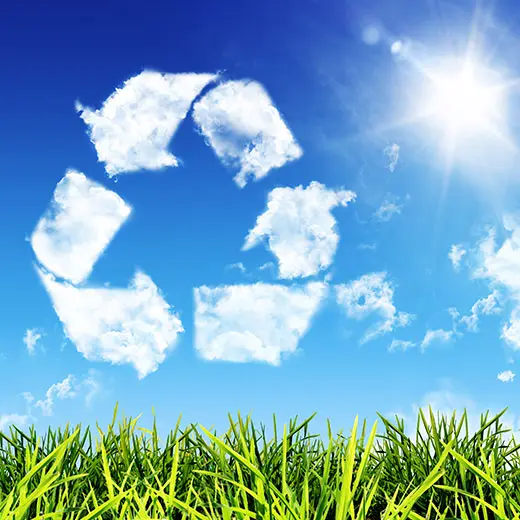
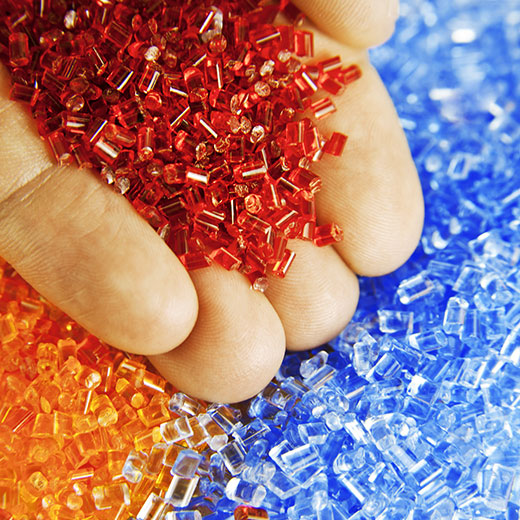
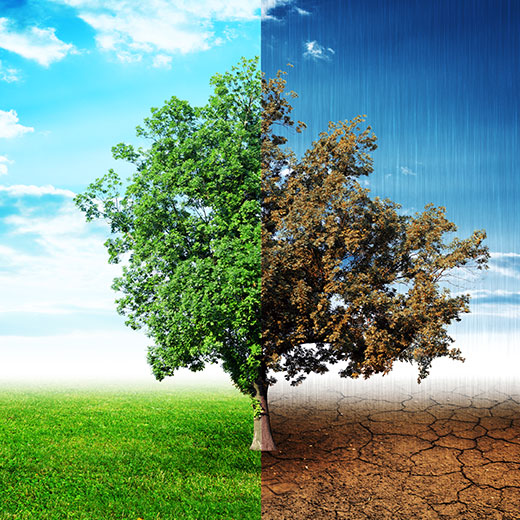
FAQ
PlasTech Mixer Melter (PMM) – Frequently Asked Questions What type of plastic can be upcycled by the PMM ?
All types of plastic from types 1 to 7 individually or mixed together (commingled)
This is revolutionary as traditional recycling technologies require the plastic waste to be sorted, washed, shredded and dried before processing, making it uneconomical to recycle and mostly gets sent to landfill or destroyed in waste to energy processes Do you need to separate the different types of plastic before upcycling them ?
The PMM is designed to handle all types of plastics, however, the more valuable polymers that are currently separated for recycling, should continue to be separated so that they can achieve their highest possible value being recycled Can the PMM recycle dirty/contaminated plastics ?
Yes, the PMM upcycles lightly contaminated plastics without the need to separate, wash and dry them.
The PMM has successfully upcycled mixed contaminated plastics from ocean, beach and river clean-ups without the need for sorting and cleaning of the materials collected Can the PMM upcycle multiple layered packaging, such as foil lined packaging ?
Yes it can. The PMM processes all multi layered packaging .. even foil coffee bags, without the need to separate them from other plastics being upcycled What other contaminants can the PMM handle ?
The PMM is primarily designed to upcycle plastics, however our R&D efforts have successfully upcycled many other contaminants with the plastics being processed. These contaminants include, but are not limited to the following:
- Carpet Tiles
- Running Shoes
- Cigarette Butts
- Paper Coffee Cups and Labels
- Textiles
- Paint Residue
Can the PMM process both soft and rigid plastics ?
Yes, the PMM can process both soft and rigid plastics of all types either individually or all together at the same time (i.e. commingled) Is the melted plastic made by the PMM mixed thoroughly or is it more like a nougat ?
The PMM mixes and melts plastics into a homogenous substrate ready for moulding What can you make from the plastic that has been processed by the PMM ?
The melted plastic from the PMM can be moulded to produce all kinds of useful products including, but not limited to, the following:
- Posts, Bollards and Rails
- Planks of all shapes and sizes for fencing or making furniture
- Sleepers and Garden Edging
- Tiles and Pipes
- Car Park Bump Stops and Speed Humps
The types of products and applications are virtually limited only by your imagination What size is the PMM ?
The technology is scalable to meet many user requirements from small (cottage) industries to very large commercial applications.
The first commercial PMM is about the size of a semi trailer and is rated to be able to recycle/upcycle up to 7000 metric tonnes of plastic material per annum. Large industries can utilise multiple machines or invest in a model designed and scaled to meet their needs. Is the PMM expensive to operate ?
The PMM uses less energy than traditional recycling methods, saving approximately $600 AUD per tonne in processing costs
The design is robust and has very few moving parts, further reducing operating costs Does the PMM create pollution ?
The PMM process create similar gases from the material to the production of virgin polymers, all of which can be captured and treated to meet the most stringent of environmental regulations. Of note, the PMM process efficiently uses electricity and frictional heat, not gas or other fossil fuels, to generate the heat to melt the plastic Who invented the PMM ?
An engineer and inventor named Ross Collins from Echuca in regional Victoria, Australia
Ross also invented a process to manufacture agricultural pipes from plastic milk bottles and a world’s first range of self-priming agricultural pumps. Can the plastic produced by the PMM be recycled ?
Yes, R&D testing has proven that plastic upcycled by the PMM can be recycled many times over without losing significant structural integrity.
Apart from the obvious benefit, it means that there is little to no waste in the PMM recycling process Who is likely to buy a PMM ?
Market research indicates the following target markets currently exist:
- Local Governments
- Waste Companies ( often contracted to local governments )
- Existing Plastic Product Manufactures to reduce manufacturing costs
- Large Companies that can recycle plastic waste in-house
- River and Ocean Clean Up Organisations
- Humanitarian Organisations
- Established Environmental Groups
- New market entrants to recycling or plastic product manufacture
What is the expected return on investment from a PMM ?
There are many variables, but our modelling suggests that ROI can be achieved in as short a time as 12-18 months depending on hours of operation, the type of product/s being produced and other local factors What other equipment is required to manufacture plastic products using a PMM ?
The size of any operation would be governed by the vision of the enterprise.
However, in addition additional equipment to basic materials handling equipment such as a fork lift and pallet racking etc.
Upstream of the PMM will require:
- a bailing facility ( unless raw materials are supplied in bales ),
- a loading mechanism such as a crane.
In line with the PMM will require:
- a gas capture/venting system to meet local regulations
Downstream of the PMM will require:
- an extruder barrel or pumping mechanism to transfer the molten substrate to the moulding equipment
- Moulding equipment such as extrusion or intrusion line etc.
- A Water tank and chiller plumbed ( recirculating) to a cooling bath
What size factory will I need ?
The size of any operation would be governed by the vision/scale of the enterprise, however a factory size of 500 mt would suffice for typical operations. Other important factors to consider are:
- Location and availability of raw materials supply
- Storage of raw materials
- Location to end markets
- Storage of the products produced
- Frequency of turnover ( freight and seasonality )
- Type of moulding equipment used
- Allowance for expansion
How many people are required to run a PMM ?
A single operator can run the PMM from loading of baled plastics through to the commencement of a downstream moulding process. Where can I find more information ?
More information can be obtained by contacting PlasTech Recycing Pty Ltd via email info@plastechrecycling.com or use our contact page
We look forward to being of service to you.